材料力学の中でも、はりにかかる力の分析はとっても大事なポイントです。
曲げ応力ってざっくりわかっているけどどう考えたらいいのかいまいちピンとこない方、実は結構いらっしゃるのではないでしょうか(過去の私がそうでした!)。
そこで今回は、せん断力図(S.F.D)と曲げモーメント図(B.M.D)の内容を一部使いながら、はりの変形や強さ、そして曲げ応力について、わかりやすくお話ししていきます。
難しそうに見える図や計算式も、ちょっとしたコツをつかめば意外とスムーズに理解できるので、ぜひ一緒に学んでいきましょう!
はりの曲げ応力と変形について
はりに荷重がかかると、はりの内部では「せん断力」と「曲げモーメント」という力が発生して、これがはりをぐっと曲げる原因になります(はりを曲げるような力が働きます)。
下の図は、長方形のはりに集中荷重がひとつ作用したときの様子です。
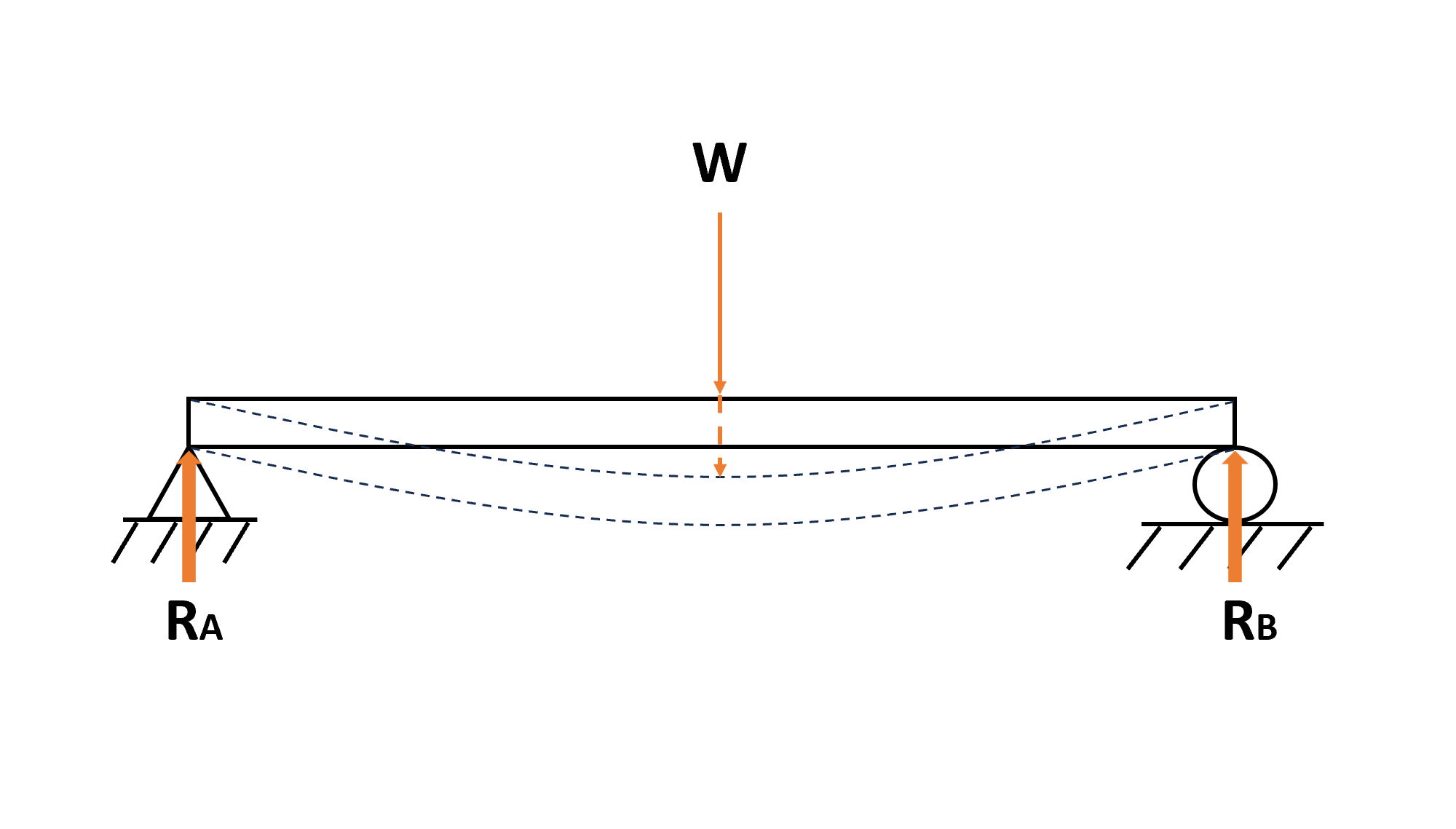
まず、せん断力図(S.F.D図)というのは、はりの断面に対して垂直に加わっている力(せん断力)が、はりのどの部分でどれくらい発生しているかを表すための図です。

ここで、はりの長い方向を何枚も薄くスライスしたようなイメージをすると、曲がろうとしている内側では材料がぐっと圧縮され、外側では引っぱられるように力がかかっているのがわかります。そうやって起きる“ずれ”のことをせん断力と言い、部材を変形させる原因のひとつになります。

図で表すと、スライスした部分(オレンジ色)の内側には圧縮応力、外側には引張応力が発生します。
それから、曲げモーメント図(B.M.D図)では「はりがどのくらい曲げられているのか」という曲げの強さの分布を視覚的につかむことができます。
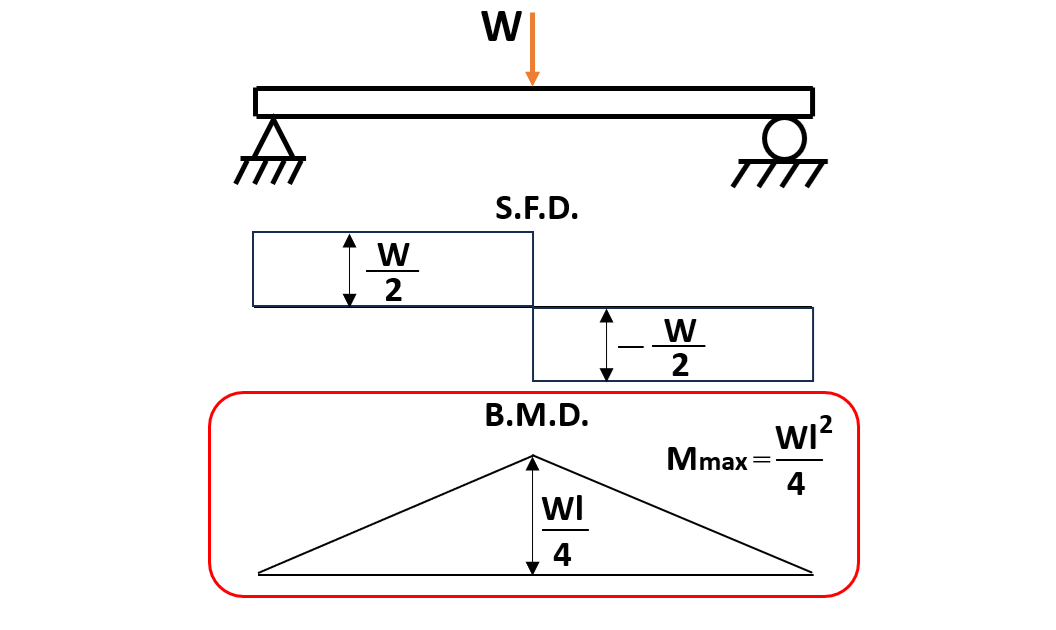
この曲げモーメントが大きいほど、はりの内部では曲げ応力が大きくなります。このことから曲げ応力とは、圧縮と引張の両方を生み出すような力のことをいい、はりの強度計算をするうえで重要な要素のひとつとなります。
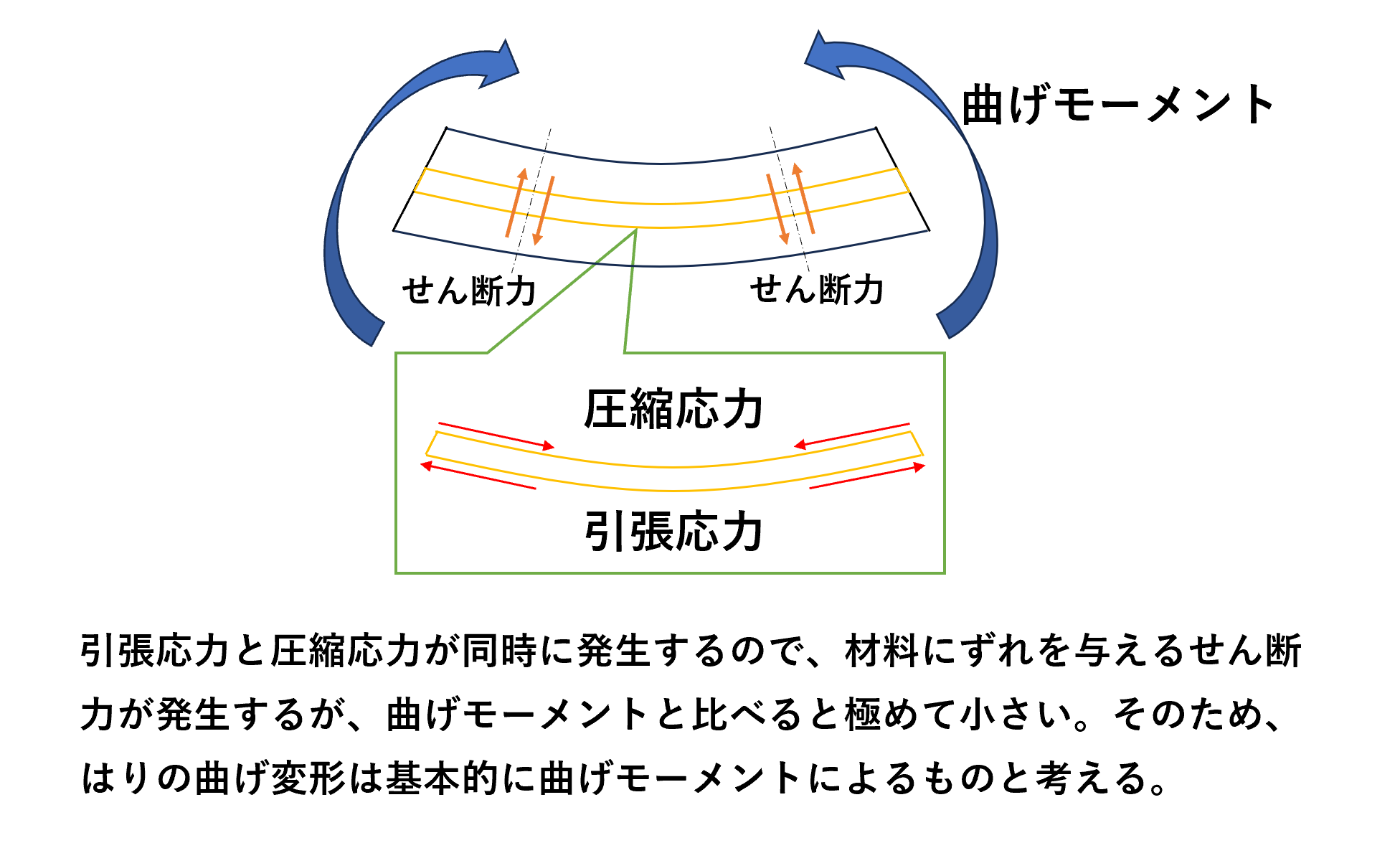
ただ、はりの中で同時に発生しているせん断応力と比べると、曲げ応力のほうがずっと大きな影響を及ぼすことが多いんです。つまり、せん断応力は曲げ応力と比べるとかなり小さい力のため、材料力学では一般的にはりの強さと曲げ応力の関係を考えていきます。
だから、材料力学では、はりの強さを考えるときに「まずは曲げ応力をどうやって小さく抑えるか」を重要視するのが一般的です。
もちろん、せん断応力が問題になる場合もありますが、ふつうは曲げ応力のチェックをしっかり行うことがはり設計のカギになるわけです。
最後に、材料の内部をもう少し詳しく見てみると、圧縮応力がかかる側と引張応力がかかる側がはっきり分かれている境目みたいなところがあります。このちょうどはりの中間あたりには、圧縮も引張もゼロになる「中立軸」と呼ばれるラインがあって、この上下で引張に変化するか圧縮に変化するかの性質が変わってくるんです。ここについては、後ほど詳しく説明しますのでお楽しみに。
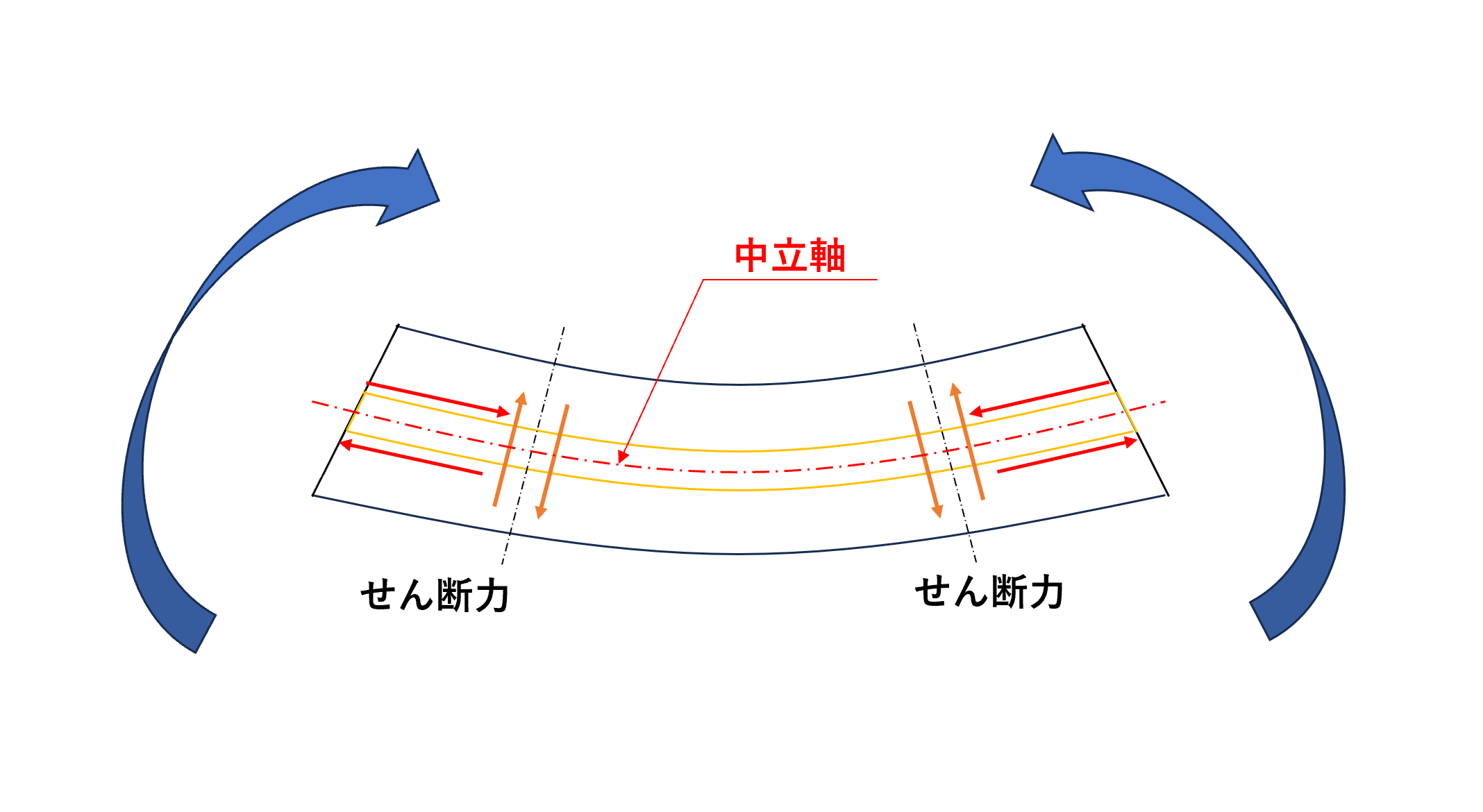
こうした力の分布をしっかり理解しておくことで、はりの強さや変形を正しく予測できるようになり、実際の設計にも役立てることができますよ。
はりの断面形状について
はりの荷重条件が限定されれば、断面積が大きいほど強度があると考えられます。
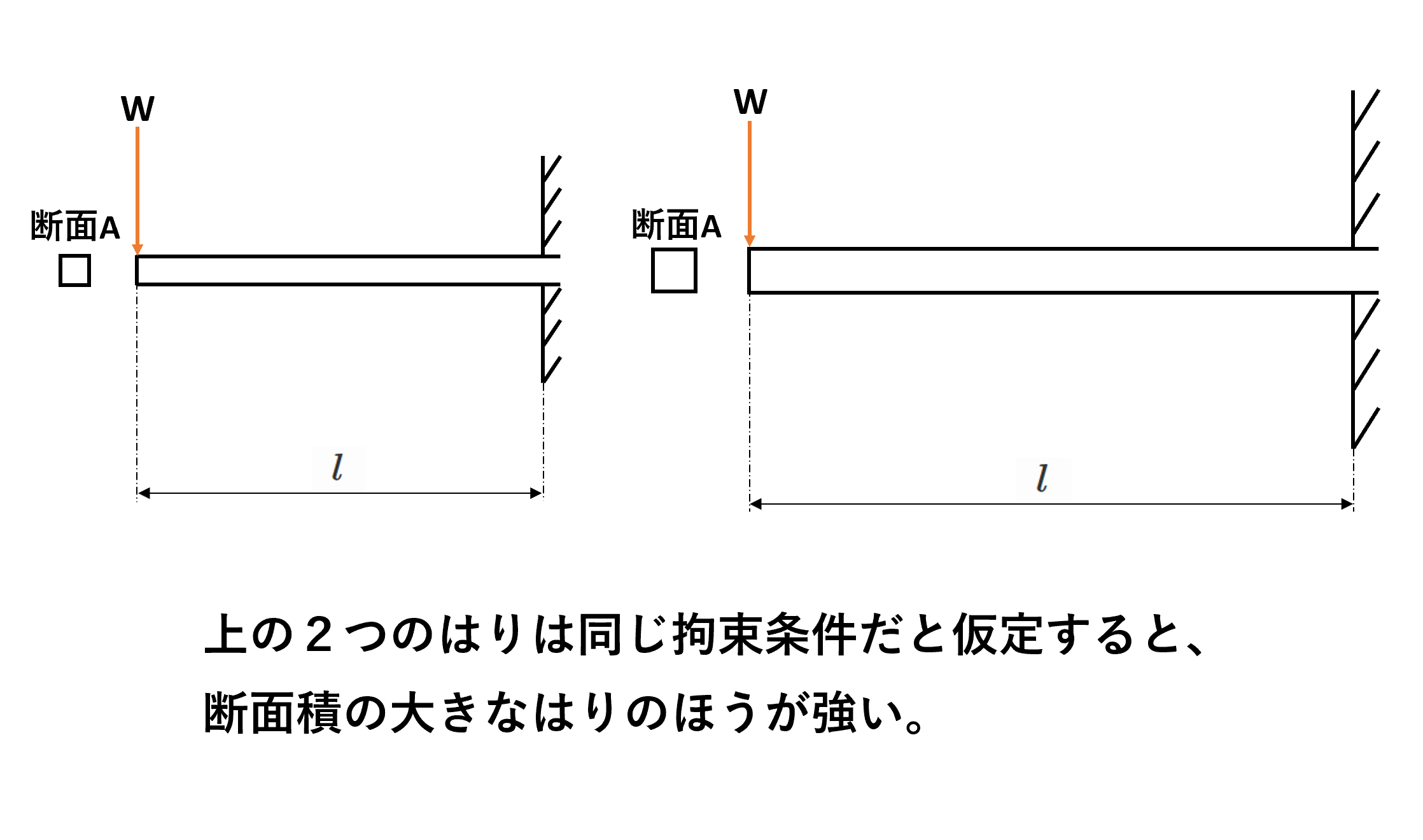
長方形断面の材料では、荷重に対して横長断面で使用するよりも、縦長断面で使用したほうが強度のある材料だということは私たちの身の周りの製品からイメージできますね。
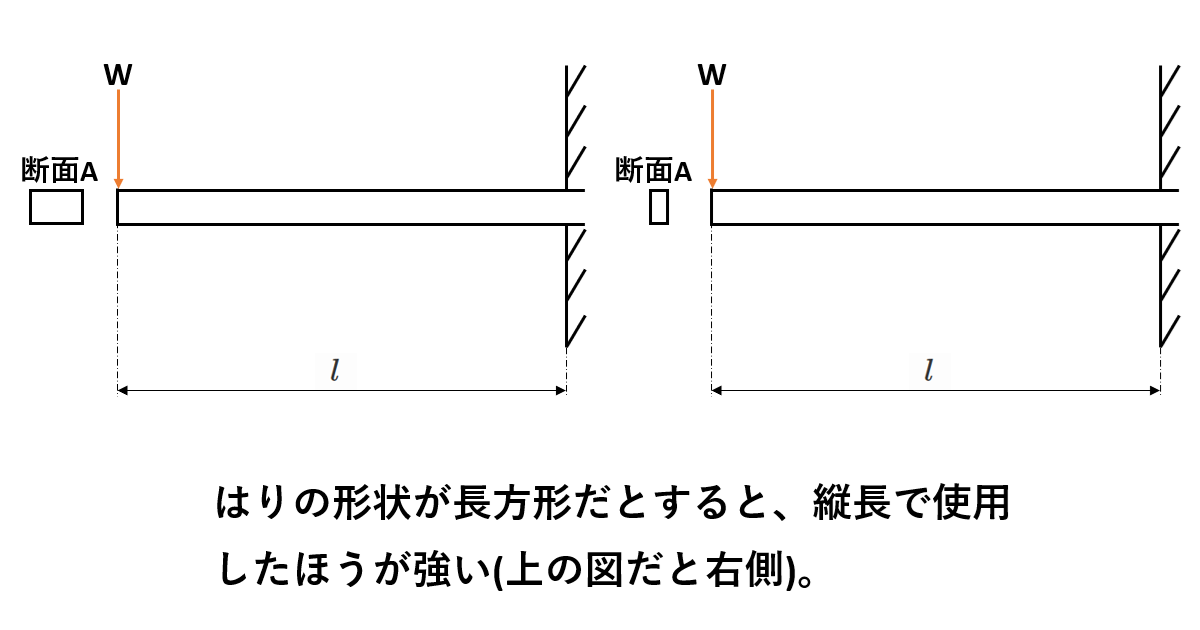
また、はりの強度は、はりの断面積と断面形状から荷重を受けるはりに発生する曲げ応力から知ることができ、はりに許容できる曲げ応力を設定すれば、荷重条件からはりの断面寸法を決定することができます。
たわみとたわみ曲線(はりの変形について)
「はり」という部材は、荷重がかかったときに内部で引張力や圧縮力などの内部応力を受けながら、全体としては曲がるように変形します。このように、はりが外力によって曲げられた結果として生じる変形や、その変形の大きさのことを「たわみ」と呼びます。たわみが大きいほど、はりは目で見てもわかる程度に曲がっていることになりますが、必ずしも肉眼で明確にわかるほどの変形だけを指すわけではなく、計算によってわずかな変形量も評価することができます。
さらに、変形後のはりの軸線にあたる部分を辿ると、元の一直線だった軸が曲線状にたわみます。この変形してできあがった軸の線のことを「たわみ曲線」と呼びます。たわみ曲線は、はりの支点条件や荷重のかかり方、はりの材料や断面形状などによって変わります。たわみ曲線を解析することで、構造的にどれだけの余裕(安全率)があるのか、もしくはどこまでの荷重なら問題ない部材なのかを判断できます。
さらに、これらを活用すると、断面形状からたわみをある程度予測したり、たわみから断面寸法を求めたりすることができます。
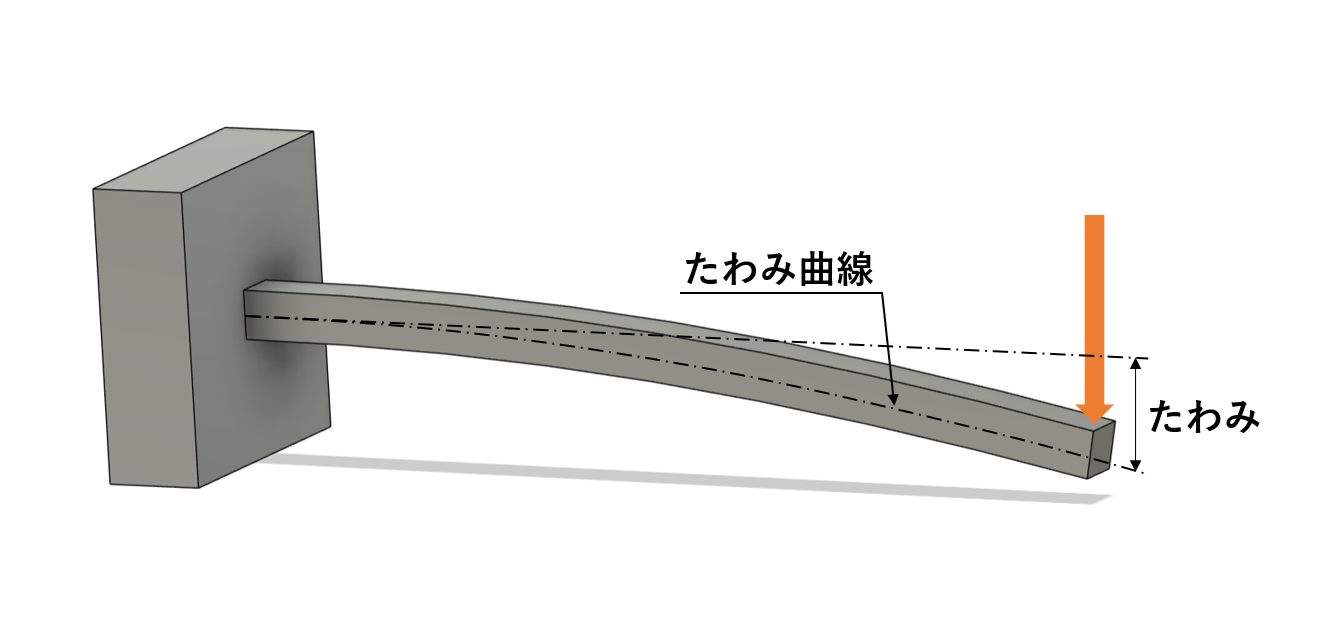
曲げ応力って?
両端支持はりの中央に外力が作用すれば、はりは下にへこむように曲がります。
曲げ荷重を受けたはりの凹側(上面)では圧縮応力が発生し、凸側(下面)では引張応力が発生します。
この2つの応力を総称したものを「曲げ応力」と呼びます。
次に記載している内容は、曲げ応力と密接な関係があるものなので重要な内容です。
ひとつずつ確認しながら見ていきましょう。
中立面
曲げ応力が発生したとき、はりや材料は下の図のように変形します。
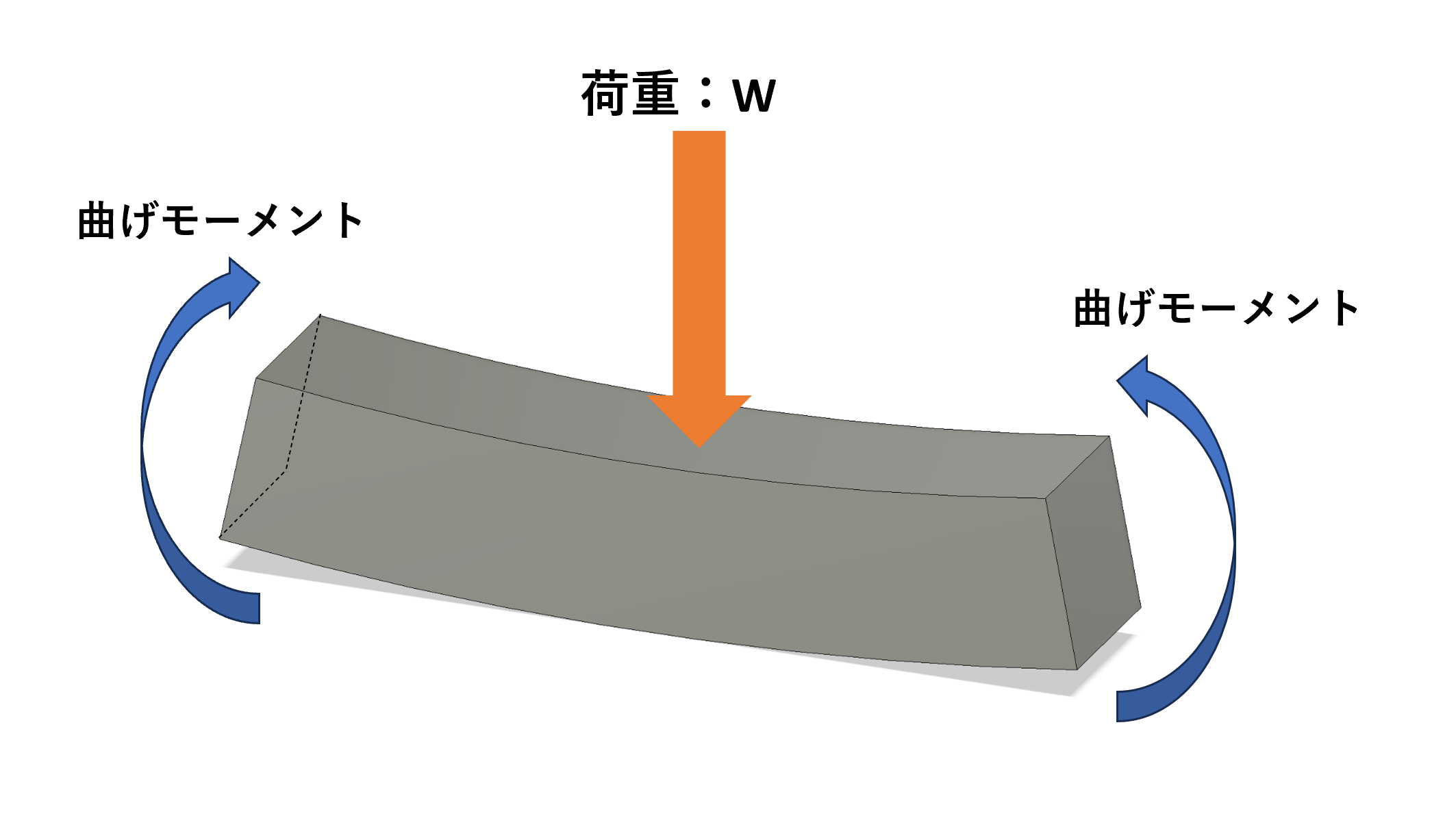
この時、曲げられたはりの内側の距離をABとすると、ABは圧縮応力によって縮みます。
反対に外側の距離をCDとすると、CDは伸びます。
内側(AB)と外側(CD)の両面からはりの真ん中に近づいていくと、変形量は徐々に減少していきます。
そして、はりのちょうど中央部分の面では、伸びも縮もしない完全な中立となる面が存在します。この面のことを「中立面」と呼びます。
また、はりの断面と中立面の交線のことを「中立軸」と呼び、任意の断面の重心をつないだ線のことを「縦主軸」といいます。
ちなみに、たわみ曲線を扱う際は、基本的に中立面を基準に考えていきます。
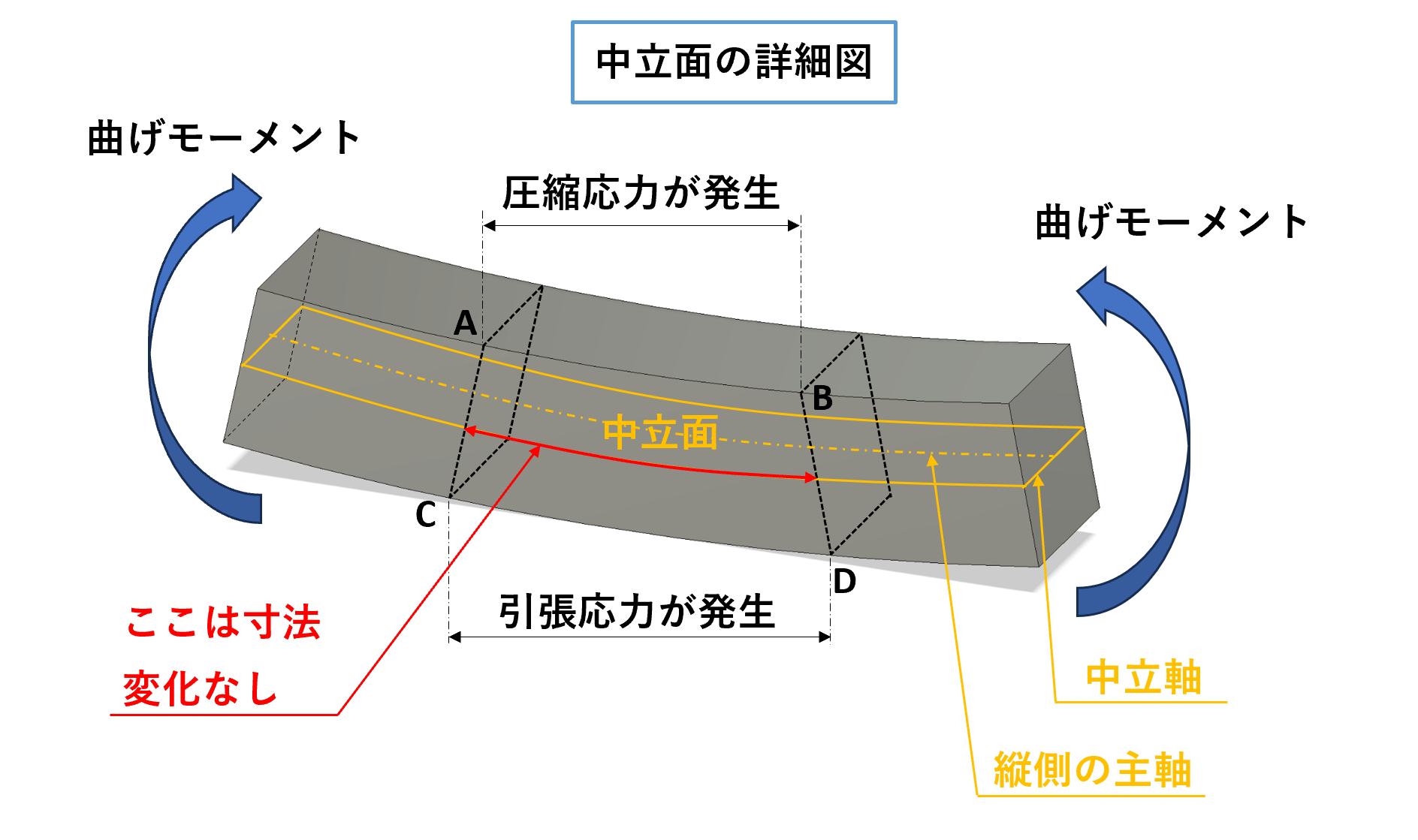
曲げ応力とひずみについて
曲げ応力が発生するとき、はりは円弧状に変化すると考えます。
下の断面図を見てください。
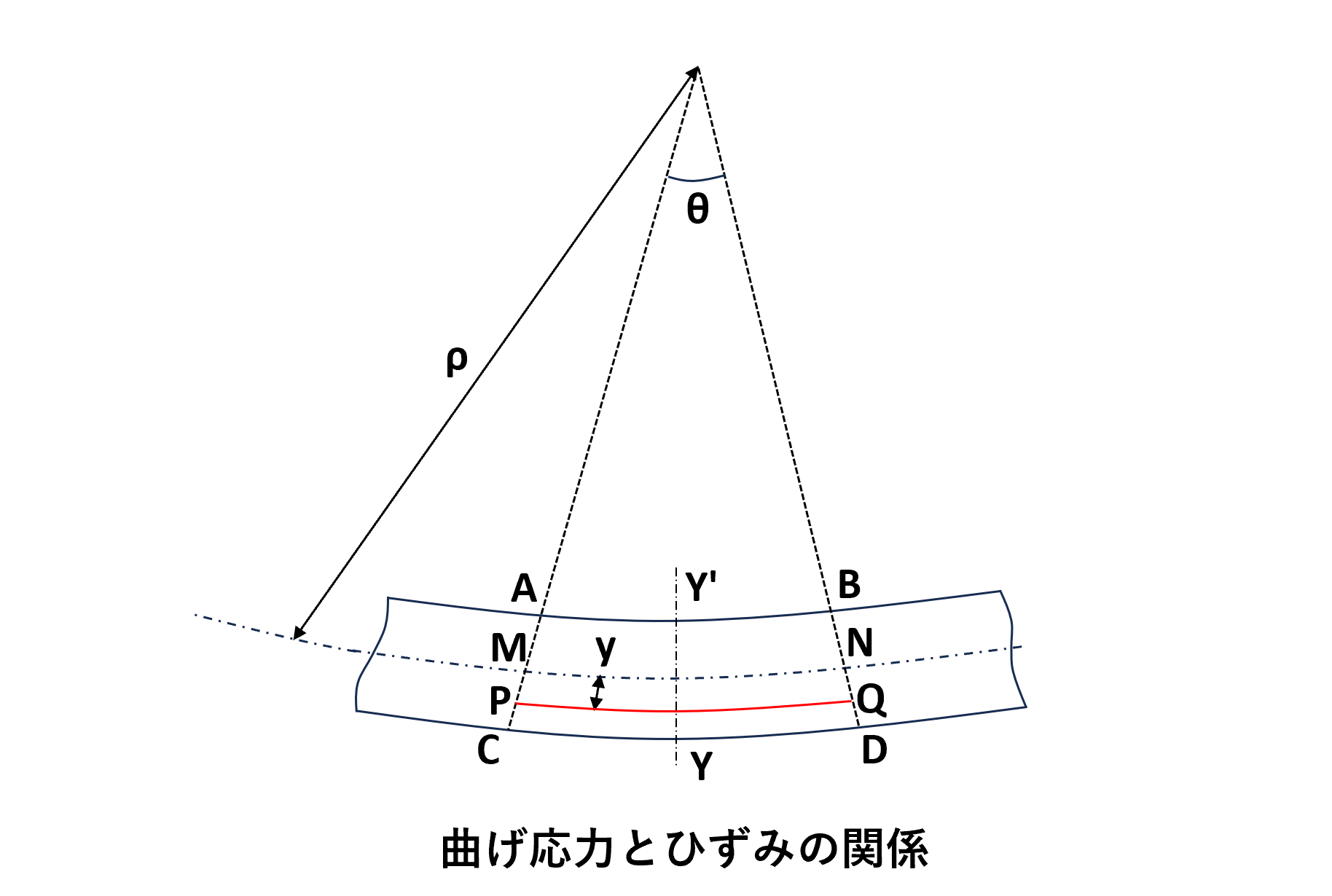
中立面MNの長さは変わらず一定です。先ほど解説しましたよね。
そして、中立面から距離yの面PQのところでは、PQの長さからMNの長さを引いた寸法の変化が発生します。
ここで、この寸法変化分をもとの長さで割ると、何が出てくるでしょうか?
実はこれ、縦ひずみεになります。
式で表すと、
$$ε=\frac{λ}{l}=\frac{PQ-MN}{MN} ・・・(1)$$
となり、元の式が縦ひずみになっています。(ひずみについておさらいしたい方は下の記事を参考)
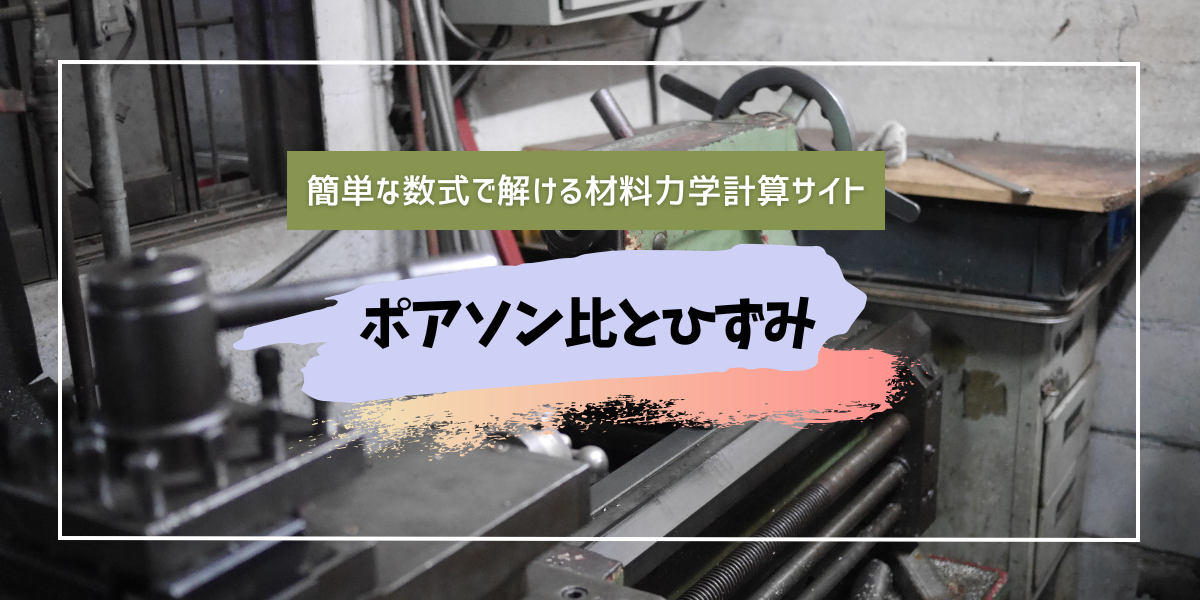
また、MNとPQは円弧の長さとなっていることから、
$$MN=ρθ ・・・(2)$$
$$PQ=(ρ+y)θ ・・・(3)$$
と立式できます。(ρ:曲率半径、θ:角度)
ここで、求めた式(2)と式(3)を式(1)に代入して縦ひずみεを求めます。すると、
$$ε=\frac{PQ-MN}{MN}$$
$$ε=\frac{(ρ+y)θ-ρθ}{ρθ}$$
$$ε=\frac{yθ}{ρθ}$$
$$ε=\frac{y}{ρ} ・・・(4)$$
が得られます。
最後に、フックの法則を応力-ひずみ線図にあてはめて考えると、
$$σ=Eε$$
$$曲げ応力σ=E\frac{y}{ρ} ・・・(5)$$
がもとまり、この式(5)が中立面から距離yにある面に発生する曲げ応力となります。
曲げ応力の大きさを定義する場合の考え方
先ほど求めた式(5)は、中立面から任意の距離yにある面に発生する曲げ応力の大きさが、距離yに比例することを表しています。
ここで、仮想断面Y-Y’を用意し、中立面を基準として凸側(下面)のyの符号を「+」、対面の凹側(上面)を「-」と設定し、yの範囲を$-e_{2}≦y≦e_{1}$とします。
yの値は材料の表面で最大となり、引張応力が発生しているほうの曲げ応力をσ_{t}、反対に圧縮応力が発生しているほうの曲げ応力をσ_{C}とすると、この値は下の図のように曲げ応力の最大値となります。
この応力のことを「縁応力」と呼びます。
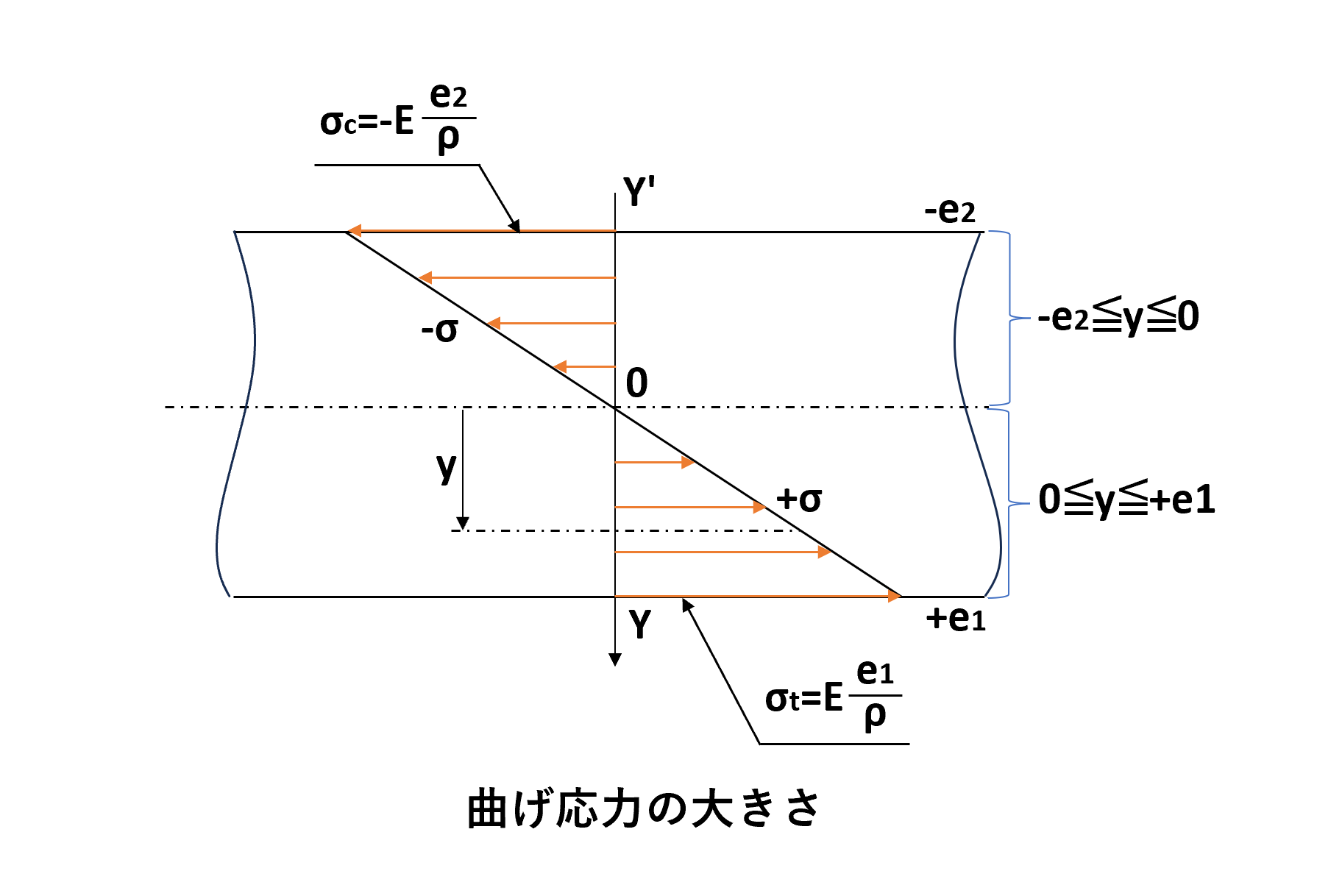
縁応力を求めるには、式(5)の、
$$曲げ応力σ=E\frac{y}{ρ}$$
を使います。
ここで、縦弾性係数Eと曲率半径ρは一定の値をとるため、応力は中立面からの距離yに比例します。
yは材料両側の表面で最大になるので、このyの数値が一番大きくなるところが縁応力を求める式となります。
部材が壊れないか?安全かどうか?を判断するには「縁応力」をみるといい!
曲げ荷重を受ける部材が弾性状態にあるときは、まず中立軸上の応力はゼロであり、中立軸から離れるほど応力が大きくなります。そして最も外側である表面(上端や下端)では応力が最大値に達します。
部材の安全性を評価するには最大応力がかかる場所を特定して管理することが重要で、曲げを受ける部材の場合、その最大応力は表面(縁)に発生するため、そこを注意深く監視すれば部材が壊れないかどうかを判断することができます。
これらのことから、曲がる部材においては縁応力が特に重要視されるのです。
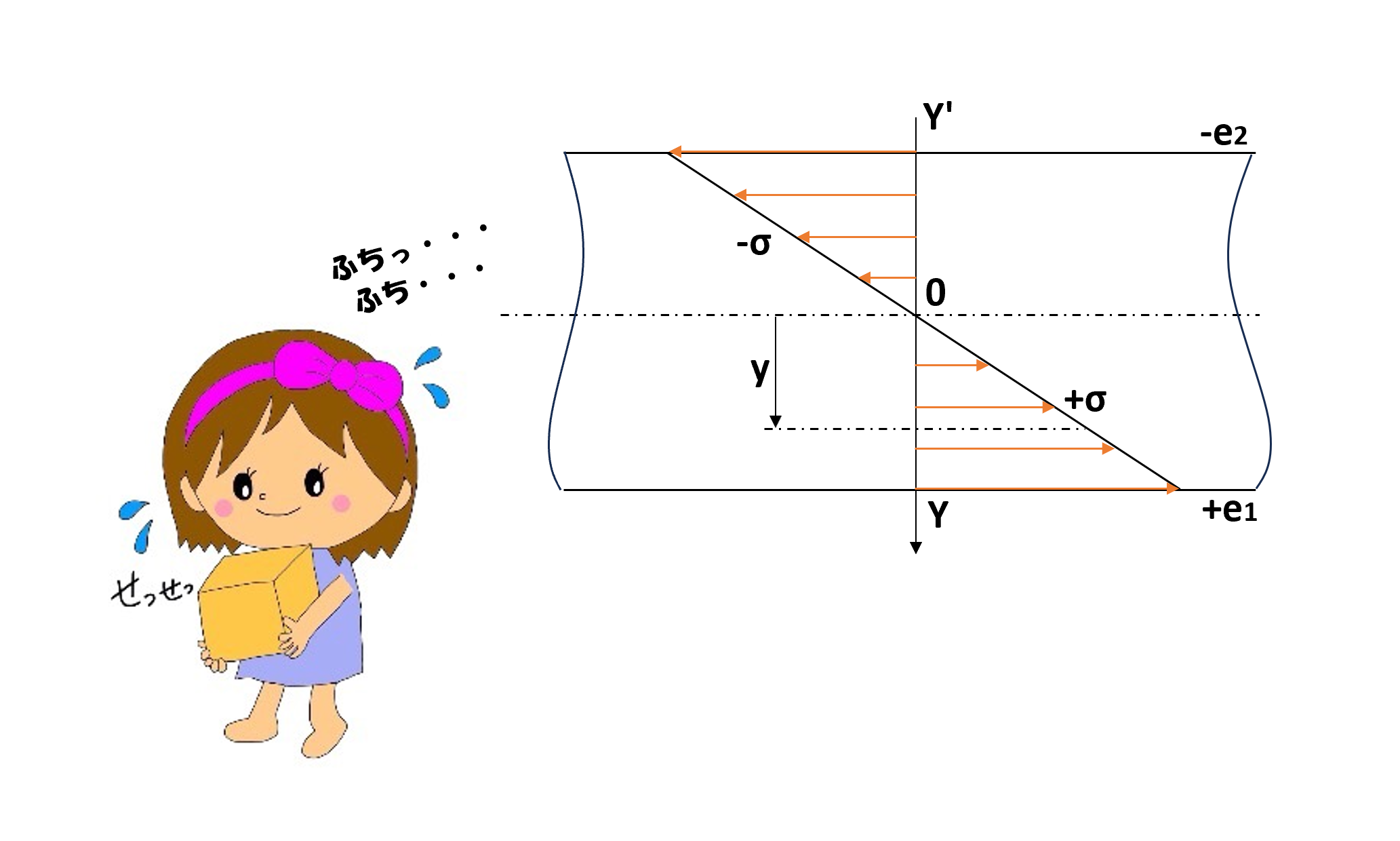
まとめ
今回の内容で、部材がどのように変形し、内部ではどのようにに応力が分布するのかイメージしやすくなったのではないでしょうか。
ここが分かれば計算はもちろん、設計や解析がよりスムーズに進むでしょう。
今回学んだポイントを基礎として、実務や学習でぜひ活用してみてください。
以上、今日はここまで!お疲れ様でした!